Skills utilized: Fabrication, CAD Design, Wiring and Electronics
At Nissan Research Center, I was responsible for integrating LiDAR sensors into the roof of a test vehicle. The design required the sensors to be adjustable, with a robust and waterproof system capable of enduring rain during testing. Years later, the vehicle remained watertight, even successfully withstanding a heavy thunderstorm.
I integrated the LiDAR sensors into a future autonomous test vehicle using custom 3D printed and sheet metal components.
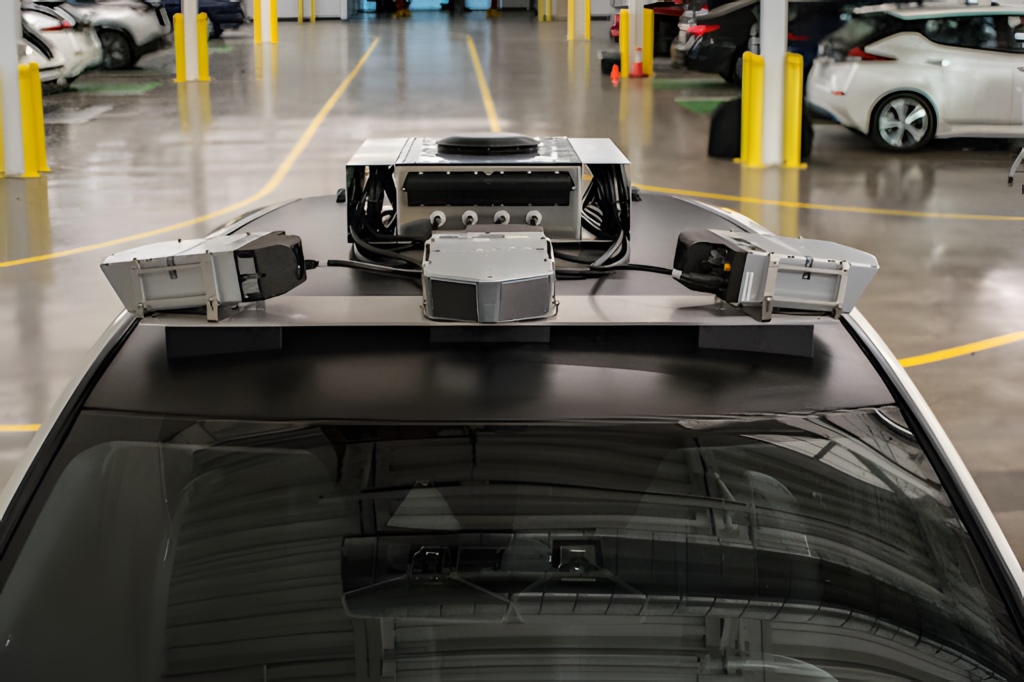
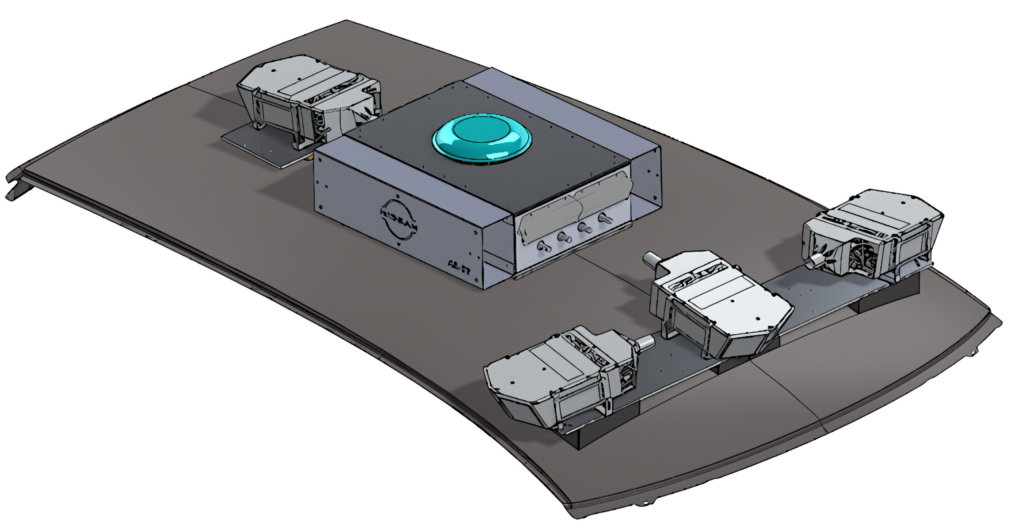
I studied the sensor Field of View in Solidworks and they were placed optimally in reference to vehicle occlusions (such as doors, roof, antennas, e.t.c.)
3D printed components were bolted to the complex roof geometry in order to create a flat, level surface for the sensors.
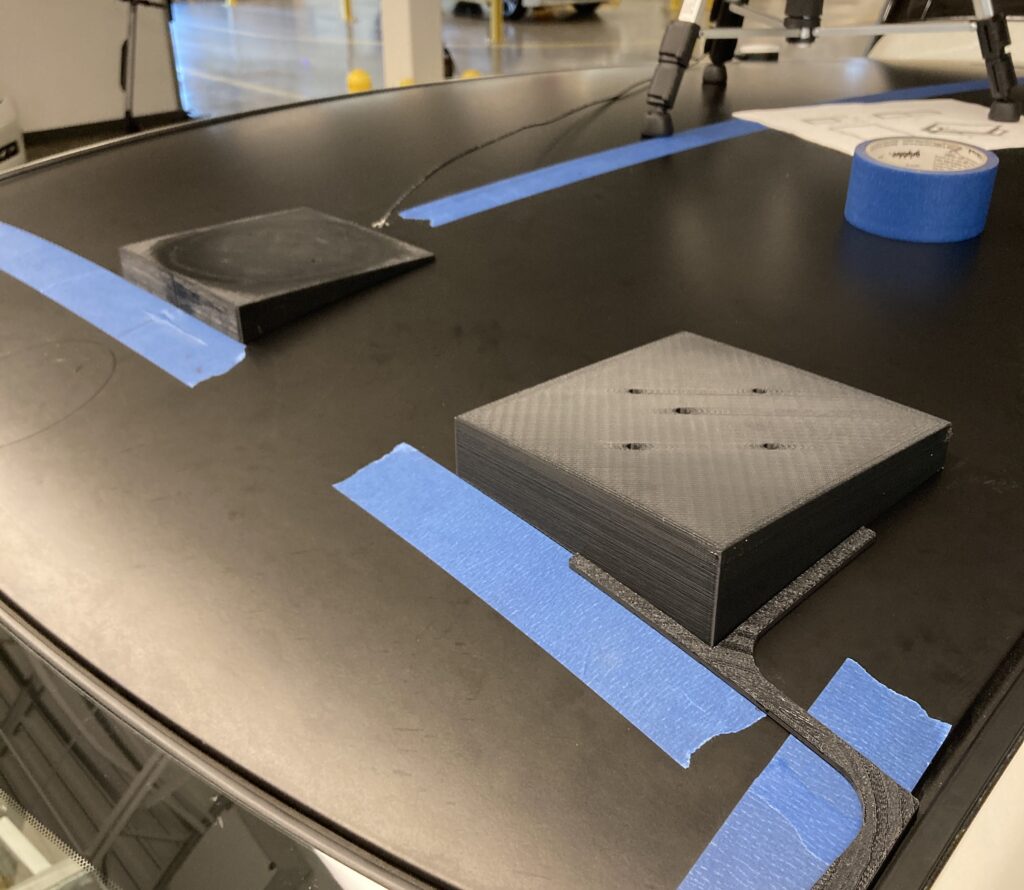
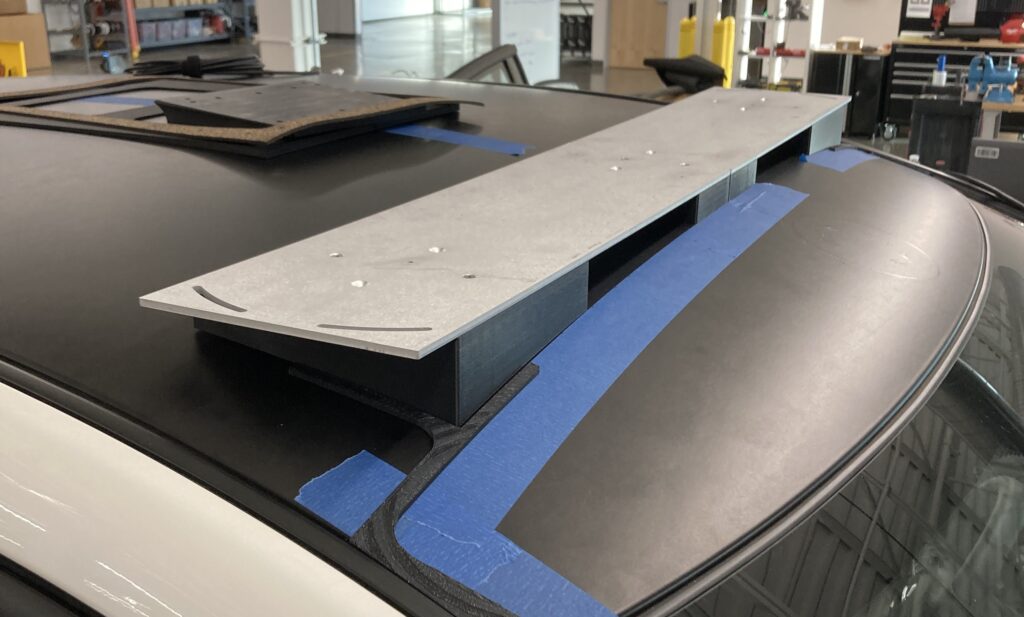
I designed a large aluminum plate to provide a rigid and adjustable yaw for each front sensor. This plate served as a reference to where the sensors were located in space, relative to the vehicle. The exact locations (+/- 2mm) were determined using a combination of laser scanning, calibration, and an old fashioned plum bob and measuring tape.
A rear 3D printed roof adapter and aluminum plate were also created for the 4th (rear) sensor.
Adjustable brackets were laser cut and bent to allow sensor pitch adjustment using the vertical slots shown to the right (for all sensors).
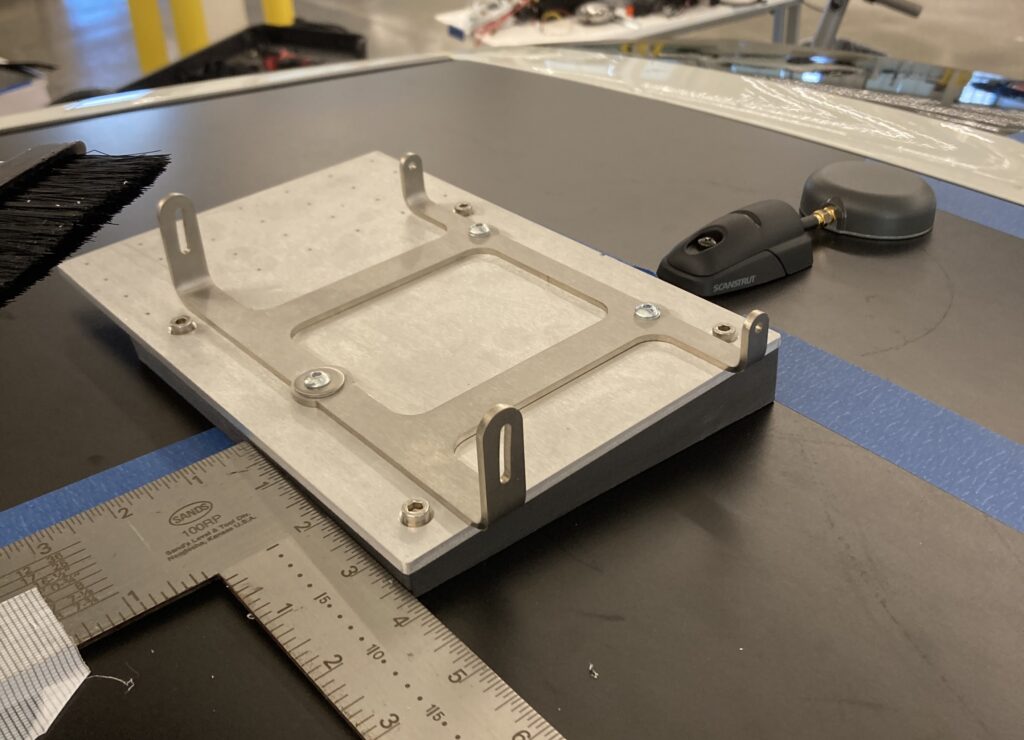
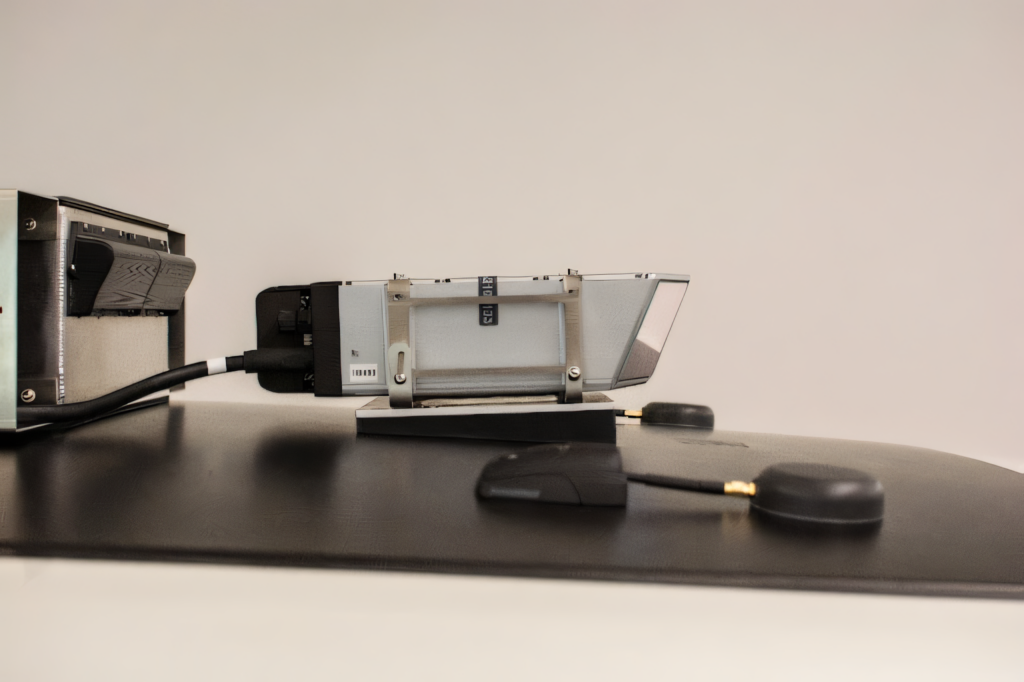
Rear sensor installed with no pitch adjustment.
The Processing PC was mounted in a similar fashion, with a 3D printed base and aluminum plate. This was mounted on the roof (compared to inside the vehicle) to reduce wiring complexity and retain waterproofing.
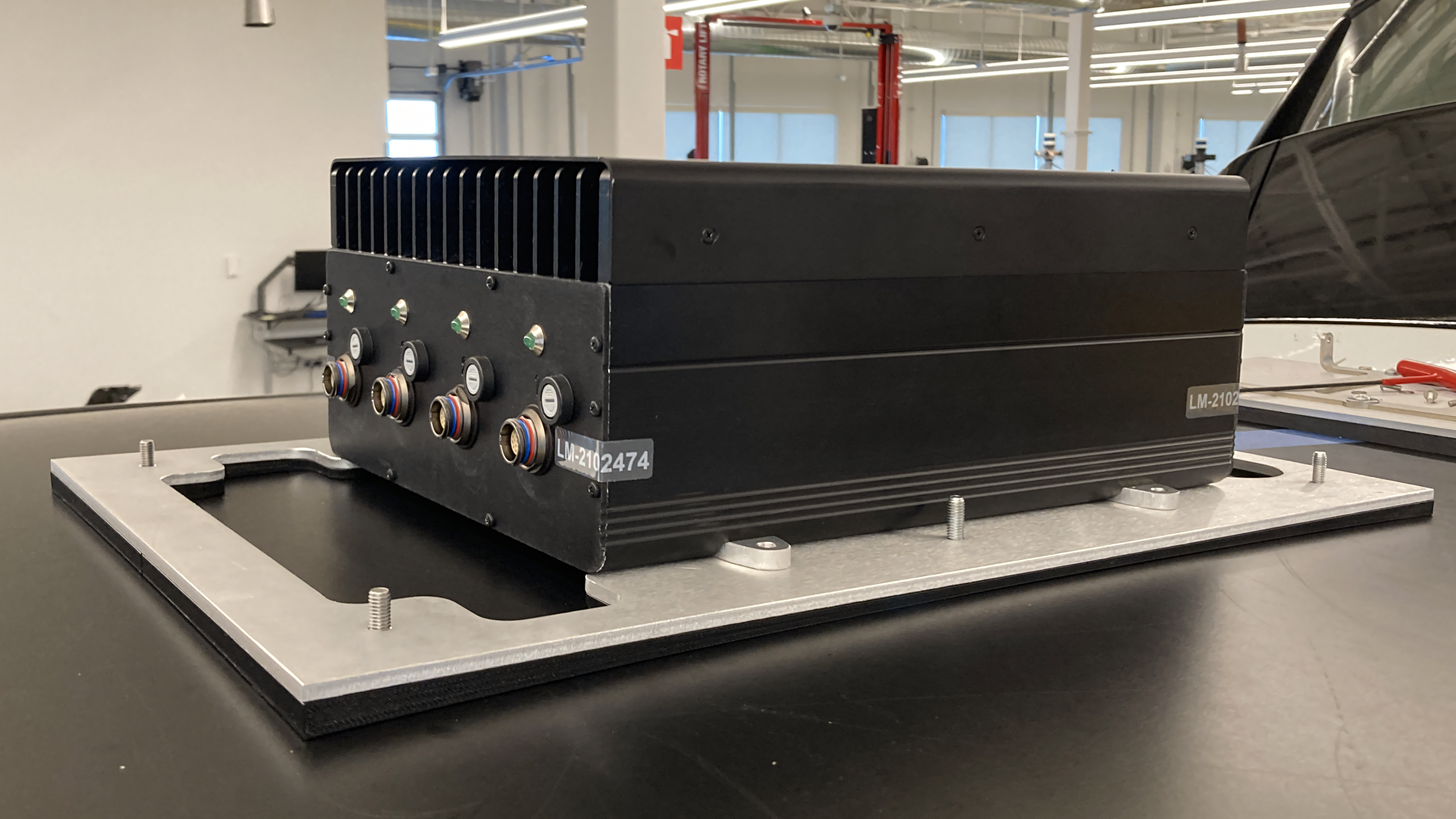
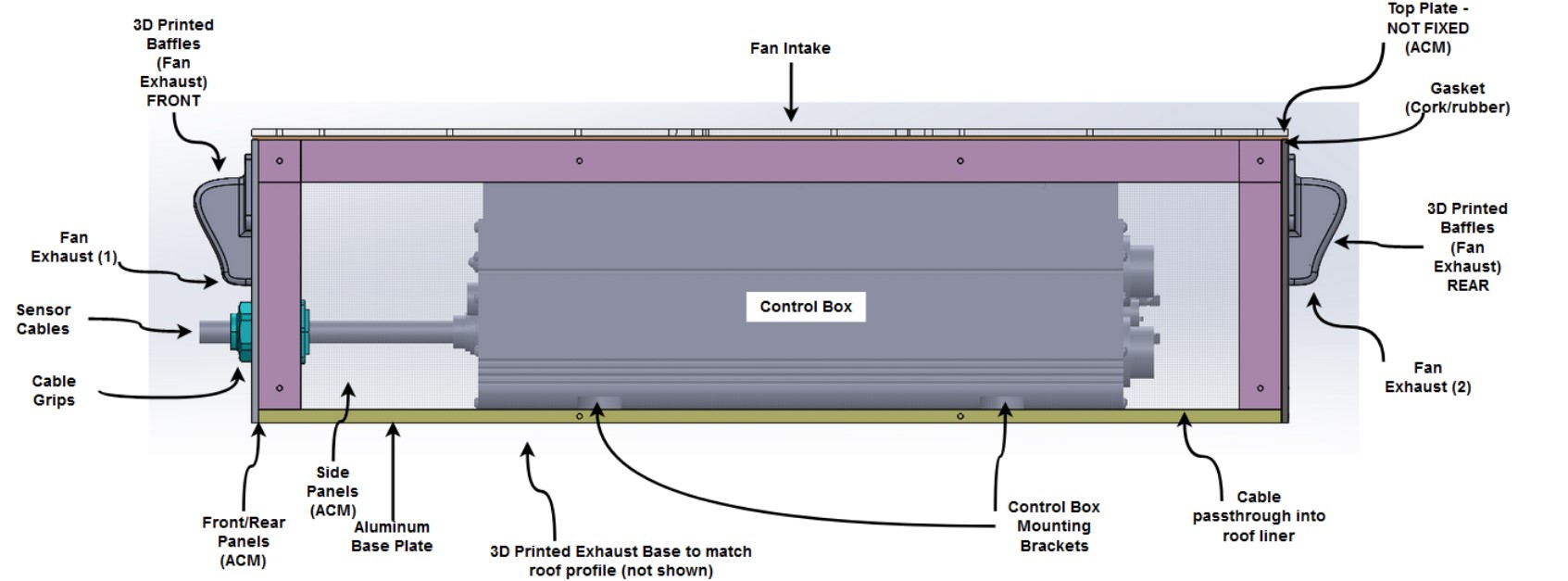
The intake and 2 exhaust baffles were 3D printed, and designed to seal against water and dust using a combination of circular gaskets and air filters.
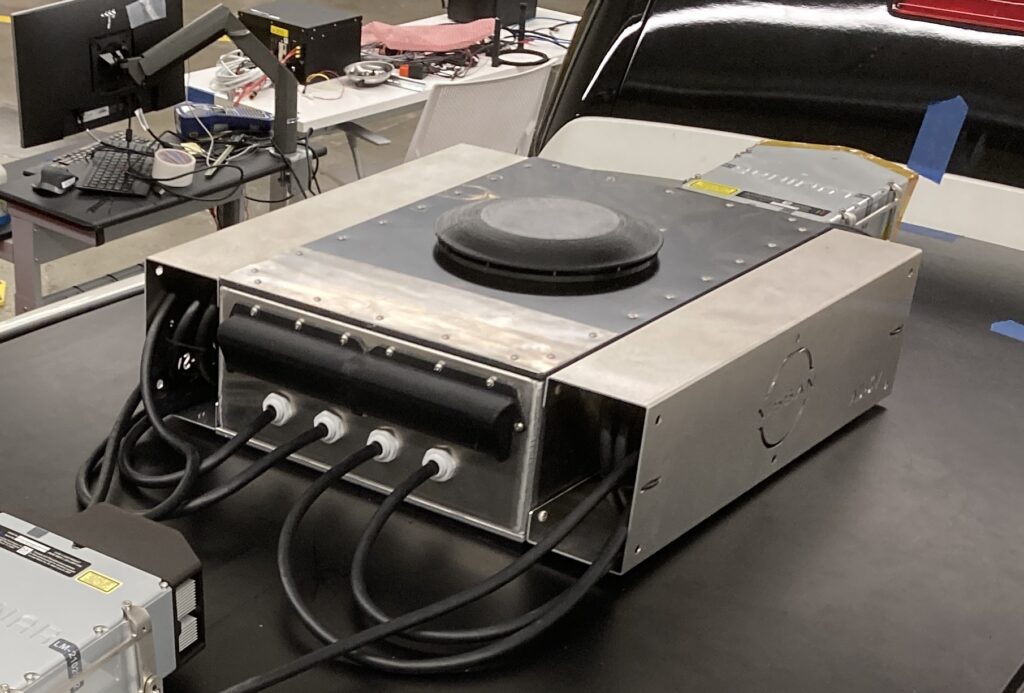
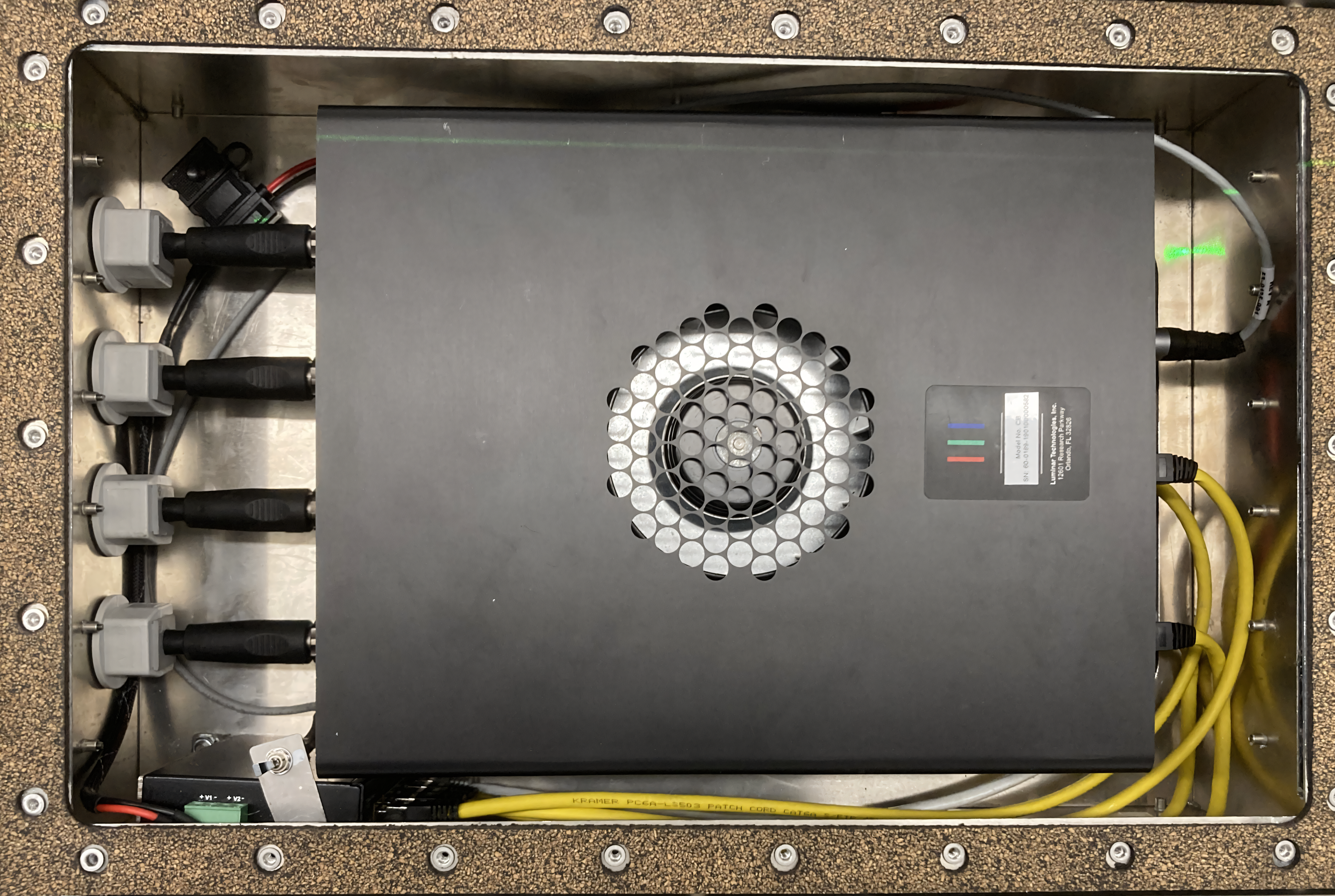
The enclosure is sealed with a custom laser cut cork/rubber gasket.
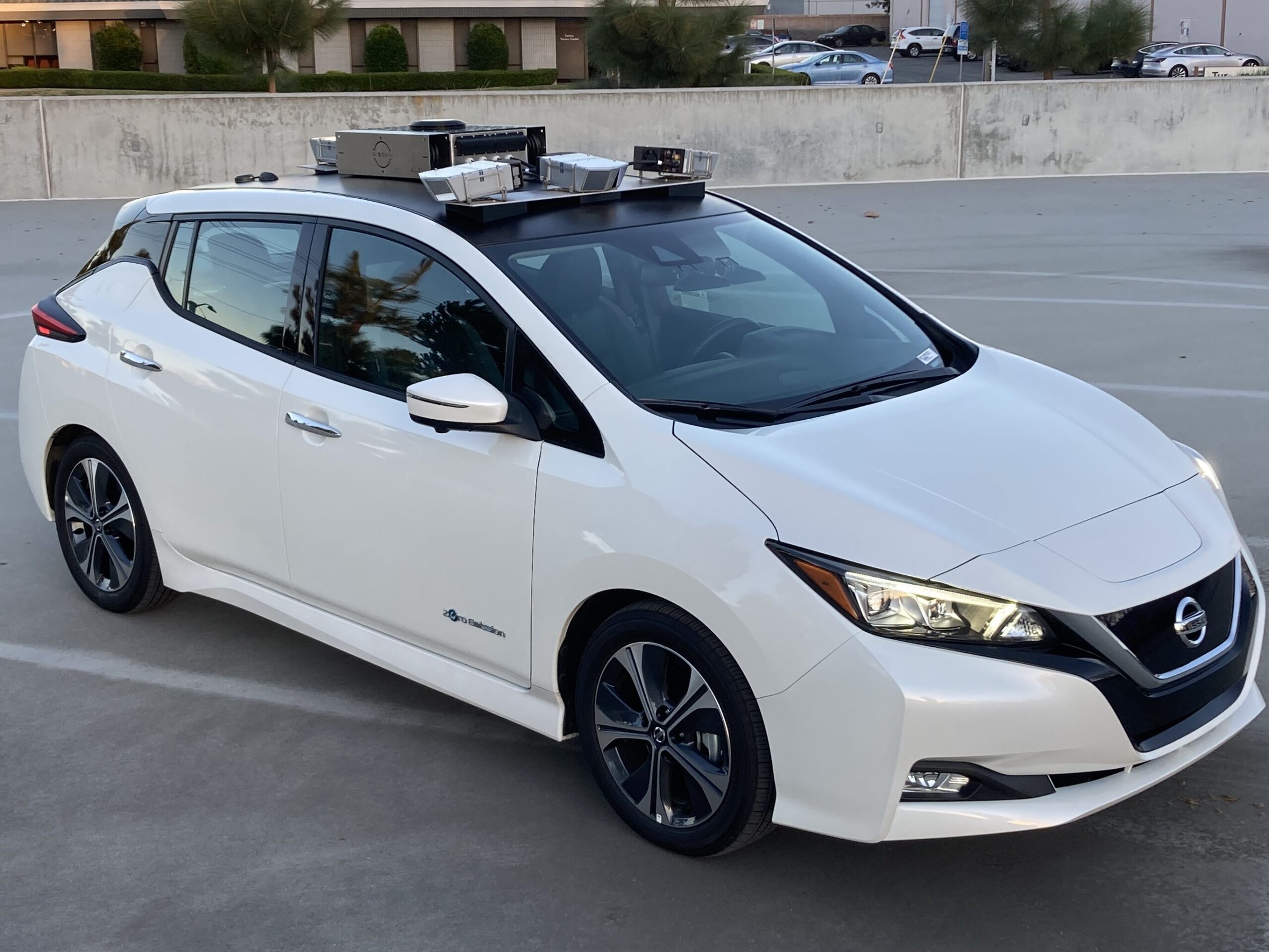